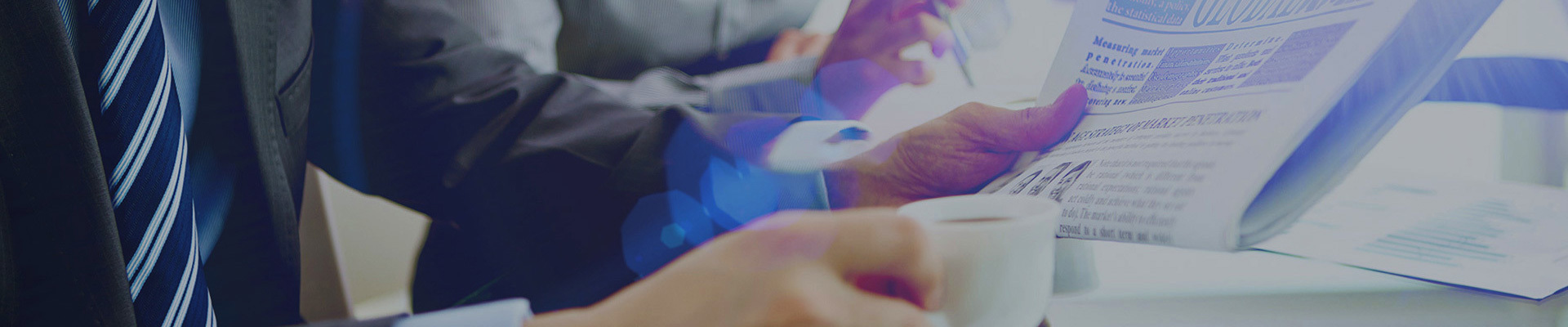
CNC machining of mechanical parts in aerospace industry
2022-06-21
Machining in the Aerospace Industry
The success or failure of aerospace operations depends on the accuracy, precision and quality of the components used. For this reason, aerospace companies utilize advanced manufacturing techniques and processes to ensure that their components fully meet their needs. While new manufacturing methods such as 3D printing are rapidly gaining popularity among industry professionals, traditional manufacturing methods such as machining continue to play a key role in the production of parts and products for aerospace applications.
aerospace engineer
Recent advances in machining techniques and technologies—such as better CAM programs, application-specific machine tools, enhanced materials and coatings, and improved chip control and vibration damping—have significantly changed aerospace companies manufacturing critical aerospace part way. However, sophisticated equipment alone is not enough. Manufacturers must have the expertise to overcome material processing challenges in the aerospace industry.
The following blog posts discuss what the aerospace component machining process includes and the machining challenges that aerospace component manufacturers face.
What does aerospace parts processing include?
Conceptually, processing raw materials into aerospace parts and products seems straightforward. However, transforming materials into functional components that fully meet application specifications and standards requires extensive engineering and operational expertise.
machining aerospace
Aerospace manufacturers often invest in CAD/CAM software and automation components for better part quality, process control and production efficiency. However, while these cutting-edge technologies help provide consistent and reliable output, company employees must have the appropriate knowledge and skills to use them effectively to machine parts efficiently.
Many critical aerospace components, such as the thermal components of jet engines, are made from nickel-based superalloys, and these aerospace materials are characterized by their ability to provide superior performance in harsh environments. This quality stems from its outstanding high temperature strength, toughness, hardness, oxidation/chemical resistance, creep resistance and thermal insulation properties. While these properties make these materials excellent choices for such components, they also make them difficult to machine. Some of the challenges faced by machinists working with nickel-based superalloys include:
Cutting force requirements are high. The high dynamic shear strength of nickel-based superalloys requires significant cutting forces to be applied to machine the material into the desired part or product.
Poor thermal conductivity. Since nickel-based superalloys do not conduct thermal energy easily, the heat from the cutting operation is transferred to the tool rather than the chip. As a result, machine tools experience greater wear in these machining operations than in machining operations on other materials.
Sensitivity to work hardening. Superalloys are prone to work hardening, leading to a greater risk of notch wear.
Given the appropriate engineering and operational expertise, machinists should be able to overcome these challenges and produce machined parts suitable for aerospace applications.